Jonathan O’Brien, CEO of Positive Purchasing, author, and global procurement thought leader, outlines his effective approach to assessing the current levels of sustainability within your supply base, then prioritizing where and how to focus your resources to make the greatest positive impact. He examines this fully in his definitive work on this fast-evolving subject, Sustainable Procurement.
Mind The Gap
You have probably determined your overall sustainability strategy. You may have implemented internal sustainability initiatives and are now looking to extend that positive impact into your supply base. What you need now is a detailed picture of what is happening in your direct supply base, once you have this you can get a true evaluation of the “gap”.
The “gap” in question is between where we are and where we want to be. This is in terms of our plan to deliver greater sustainability within our own business, and as far along our supply chain, or Supply Value Chain Network (SVCN) as I call it, as the data, time and resources available will support.
Get this right and it can provide the knowledge and impetus for effective sustainable procurement. Get this wrong and our efforts could be ineffectual or, at worst, a well-intentioned waste of effort, time and money.
Measurement
We need to establish a baseline against which we set our objectives and can ultimately measure our positive impacts (i.e. how we are closing the “gap”.
Whilst we can quantify emissions, pollution levels and resources consumed, or recycled etc, it is much harder to quantify how human rights are upheld or evaluate the quality of working conditions. We can however, assess these aspects against our own pre-set minimum requirements, an established international standard or how closely they comply with the latest legislation.
Sadly, we will never have sufficient time resources and budget to do everything, so start where there is greatest chance of successfully achieving the most important results. Liberally share the resulting learnings and the good news stories (more about this later) then work our way as far down our “Hit List“ as resources allow.
Sadly, we will never have sufficient time resources and budget to do everything, so start where there is greatest chance of successfully achieving the most important results.
How Do we Approach This?
- Identify where we have the greatest likelihood of achieving the most conspicuous and important results.
- Build an initial Hit List of the best prospective projects in order of importance.
- Create SMART goals for improving sustainability performance for those organizations on the Hit List.
- Assess the current performance of the target organizations and evaluate the gap between the current situation and your goals for each organization on the Hit List.
- Understand what is needed in terms of budget, resources, and data to achieve our goals.
- Remove those organizations it won’t be feasible to work with given geopolitical situations, resource availability and budget.
- Refine, reorder, and finalize the Hit List.
Drawing on the expertise and knowledge of the relevant team members within your organization, supplemented by some smart desk research (SSTP, PESTLE, Hot Spot Analysis) you can get a good picture of steps 1 – 3 above for most suppliers. But it is at step 4 that the rubber really hits the road as, without an accurate assessment of the current base line, your planning, and by extension your sustainability initiative, will not be effective.
Conducting A Supplier Assessment
There are broadly two ways to conduct an assessment:
- Remote – where a combination of knowledge from within your organization and any related agents and other “friendly” sources is supplemented by desk research. Remaining data gaps can then be addressed through a third-party ratings provider or via our own questionnaire based assessment.
- In-Person – For those organizations where sufficient data is just not available via remote resources, or where there is a need for a boots-on-the-ground data verification.
Always start with a remote assessment. For some suppliers this may be sufficient to get an accurate baseline reading. However, there will inevitably be those suppliers that cannot be accurately assessed using remote methods, but are sufficiently important in justifying the expenditure of resources needed to conduct an in-person assessment.
This is too complex a subject to tackle in one sitting, so I am going to address it in two parts starting with Remote Assessments.
Part 1. Remote Assessments
Once you have your initial Hit List it will be possible to gain an idea of what is needed to achieve the target results for each supplier. Bagging some early wins is great for generating those all-important good news stories. Start with those projects that will deliver significant early results. Then, using the knowledge and expertise gained, move on to initiatives whose potential results and likelihood of success, represent the best use of your available resources and budget.
The task is as much to decide what you are not going to do as what you are, so unless there are any key suppliers that you have already identified as suitable for immediate attention, look to remove the less viable suppliers early in the assessment process.
It Aint Easy…
Don’t underestimate the difficulty of carrying out this type of assessment. If your supply chain is distributed, data may be hard to get and verify. Inevitably, some individuals involved will have a vested interest in either being seen to tick all the right boxes or may even seek to conceal any detrimental aspects. Be relentless in endeavouring to understand the full picture of what is going on with target suppliers and don’t be shy about seeking all the expert help you can get.
For those areas where there is either greatest risk or greatest opportunity to achieve the most positive impact (the hot spots), it may be justified to get a first-hand, in-person assessment. Nothing beats boots on the ground with a tablet, a list of smart questions and the steely determination to get accurate answers – warts and all. However, given the relatively high level of resource an in-person assessment takes, especially in more far-flung locations, this is not always viable.
The Remote Approach
Remote assessments are our best option at present and, if done well, can be adequate for some suppliers. This can include:
- Accreditations & certification – do they meet all national, international, governing body and legislative standards?
- General research – websites, published information, supplier reports, news stories, web chatter etc.
- Remote assessment – in-house generated questionnaires, their acceptance of our codes of conduct and practice.
- Third party ratings providers – questionnaires, sustainability rating index providers, SRI indexes, supplier rankings.
With the growth in the number of companies specializing in providing supplier sustainability ratings based upon data collection via a remote questionnaire approach, measuring sustainability is becoming increasingly more possible and, whist this may not deliver 100% accurate or totally definitive results, it is certainly a very good start.
It’s now possible to augment the current range of remote assessment sources with other sources of data, including some innovative approaches such as using AI to interpret real-time satellite imagery in order to verify existing knowledge or identify anomalies.
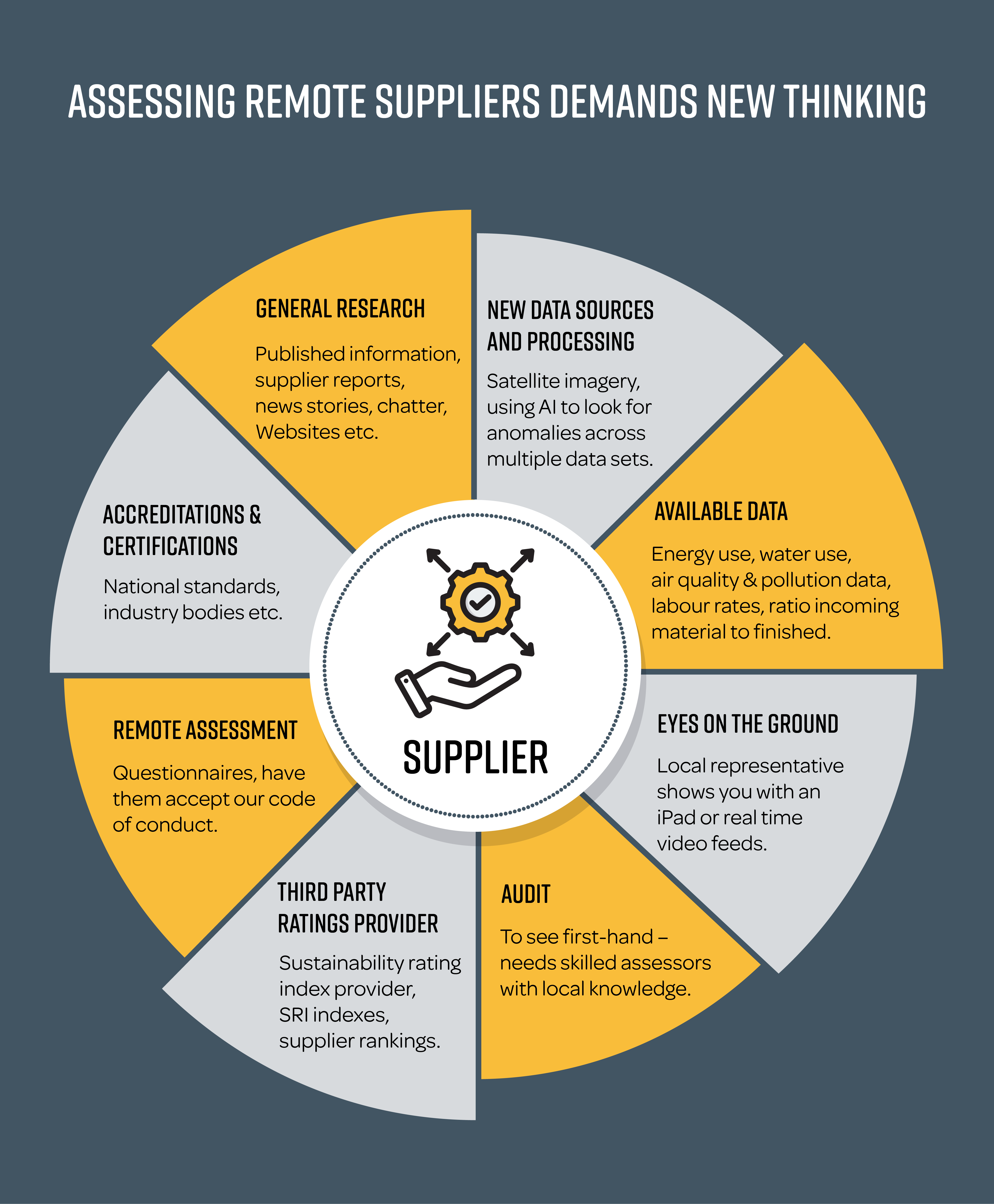
Collate the Data, Decide What You Don’t Know and In Fill the Gaps
Having completed the above steps, we should have our revised Hit List with associated SMART sustainability goals and a semi-complete contextualized data set with any gaps in essential knowledge identified. We now need to fill as many of these key knowledge gaps as possible.
Alas, there is always a “however” and here it comes; it may not be possible to get all the data you are looking for and, at a very basic level, you must rely on the accuracy and, fundamentally, the honesty of the responses you get as you have no way of independently verifying.
Needless to say, the more work you can do in-house, the further your budget will go, so it is worth either creating or expanding any internal research resources you have. As sustainability legislation increases, this area of business requirement will have to grow accordingly.
As sustainability legislation increases, this area of business requirement will have to grow accordingly.
Don’t Hide Your Light!
We have our prioritized Hit List of suppliers with related initiatives, and baseline data. We have a mandate, a budget, we’ve hit the “GO” button, our projects are delivering good results and we have regular project reviews and wash-ups to capture key learning.
Happy days!
Take and share the credit and ensure all the right people get to hear about it.
The Power of the Positive Story
Now is the time to craft good news stories that promote your achievements, demonstrate your evolving expertise and shamelessly merchandise them. Share the credit liberally, both internally (especially amongst supporting executive team members and Board sponsors) and amongst the deserving members of your SVCN, as this will motivate those involved to keep contributing and become active evangelists. If previously reluctant key stakeholders and influencers are not moved to get behind future initiatives, they should, at the very least, become less resistant.
Well merchandised positive sustainability narratives are hugely valuable given that we know:
- Rapidly growing consumer segments are choosing brands with credible sustainability credentials.
- Organizations need to mitigate the risk of negative reputational impact from the exposure of poor sustainability practices.
- Organizations need to be conspicuously on the right side of the line as new sustainability legislation is enacted.
- Investors are increasingly upweighting sustainability in their evaluations.
- Potential employees want to work for sustainability conscious companies.
- The SVCN increasingly recognizes they must adapt accordingly.
- The more valuable and wider ranging successful sustainability initiatives become (and are recognized by key stakeholders), the more resources will be made available for future projects.
There Is No More “Long Term” – So Be Ruthless
Suppliers are faced with a choice – adopt more sustainable practices or progressively lose customers.
We have a similar decision to make about our suppliers. Drive verifiable sustainable change (with our help where it is viable) or change to more sustainably responsible suppliers.
This is not an oversimplification as the reputational risk is now unacceptably high.
Sustainability detectives backed by combative eco-journalists are proliferating, seeking whistle-blowers to expose bad sustainability behaviour. Ever more sustainability conscious consumers are happy to vote with their credit cards when an eco-villain is exposed. Then, agile competitors armed with razor-sharp, cast-iron sustainability credentials charge in to subsume the vacated market share.
The fact is there will never be sufficient budget to change all your suppliers so:
- Choose sustainably effective suppliers in the first place.
- Change those you can afford to.
- Replace those that cannot or will not change.
The harsh reality is that Darwin is still right – everything must evolve or die.
This insight article is adapted from Sustainable Procurement: A Practical Guide to Corporate Social Responsibility in the Supply Chain by Jonathan O’Brien © 2023 and reproduced by permission of Kogan Page Ltd.
Jonathan O’Brien, CEO of Positive Purchasing, is a leading expert on procurement and sustainability and works with global blue-chip organizations to help transform their purchasing capability.